Manufacturing RFID tags involves several steps, generally including the following:
1. Designing: Design the RFID tag layout, antenna size, chip placement, and overall dimensions based on the intended application and frequency requirements.
2. Choosing Components: Select suitable components such as RFID chips, antennas, substrates, and encapsulation materials based on the desired performance and environmental conditions.
3. Printing Antennas: Print or etch the antenna onto a substrate material using techniques like screen printing, flexography, or lithography. This step is crucial as the antenna design affects the tag's performance.
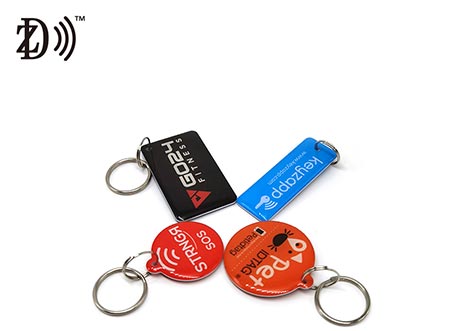
4. Attaching Chips: Attach the RFID chip to the antenna using conductive adhesive, soldering, or flip-chip bonding methods. This process requires precision to ensure proper electrical connections.
5. Encapsulation: Encapsulate the chip and antenna assembly within a protective material such as plastic, paper, or epoxy resin to shield it from moisture, temperature variations, and physical damage.
6. Testing: Test the manufactured RFID tags to verify functionality, read range, and data integrity. Quality assurance processes may include performance testing, frequency testing, and environmental testing.
7. Encoding: Optionally, encode data onto the RFID tags using RFID readers/writers. This step involves programming unique identification numbers or other relevant information onto the tags according to the specific application requirements.
8. Packaging: Package the RFID tags in suitable formats for distribution, which may include rolls, sheets, or individual units depending on the intended use case.
9. Distribution: Distribute the manufactured RFID tags to customers or end-users through appropriate channels.
Each step requires specialized equipment, expertise, and quality control measures to ensure the production of reliable and functional RFID tags. Additionally, compliance with regulatory standards and industry specifications is essential throughout the manufacturing process.