RFID wristbands are typically manufactured through a multi-step process. Here's an overview of how they are generally made:
1. Material selection:
- Most RFID wristbands are made from flexible, durable materials like silicone, PVC, or TPU (Thermoplastic Polyurethane).
2. Molding:
- The wristband material is injection molded or extruded into the desired shape and size.
3. RFID inlay preparation:
- The RFID chip and antenna (together called an inlay) are prepared separately.
- The chip is typically attached to the antenna using a conductive adhesive.
4. Inlay insertion:
- The RFID inlay is carefully inserted into the wristband. This can be done in two ways:
a) During the molding process (known as in-mold labeling)
b) After molding, by creating a pocket in the wristband and sealing the inlay inside
5. Sealing:
- If the inlay is inserted after molding, the wristband is sealed to protect the electronics from moisture and damage.
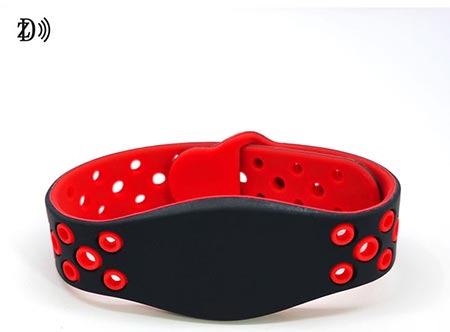
6. Programming:
- The RFID chip is programmed with the necessary data or ID number.
7. Testing:
- Each wristband is tested to ensure the RFID chip is functioning correctly.
8. Customization (optional):
- Wristbands may be printed or engraved with logos, text, or designs as per customer requirements.
9. Closure mechanism:
- Depending on the design, a closure mechanism (like a snap or sliding lock) may be added.
10. Quality control:
- Final inspection is performed to ensure the wristbands meet quality standards.
11. Packaging:
- The finished wristbands are packaged for shipping.
The exact process can vary depending on the manufacturer, the specific type of RFID technology used (LF, HF, or UHF), and the intended application of the wristbands. Some high-security applications might involve additional steps to prevent tampering or counterfeiting.